ZIPPERED WOOD
Through a process of physics simulation and computerized geometric analysis Zippered Wood enables ordinary 2x4s to be assembled in any custom twist or curvature at a designer’s disposal.
This research maintains codependency between material properties and digital simulation. Bending and twisting in wood are governed by the material behavior of wood grain. By deploying digital physics simulation, this research allows a designer to manipulate this phenomenon in the abstract. A series of geometric analysis algorithms have been developed that translate simulated twists or bends into unique joint patterns. Robotic milling transcribes these coded joints into reclaimed stock, removing the need for formwork or skilled assembly. After milling, corresponding pairs are assembled by the simple application of adhesive and pressure. Form is a result of the cumulative displacement occurring between all faces of the internal joint pattern. Zippered Wood uses a material informed digital processes to convert standard 2x4s into formally sophisticated building components. Refinements are underway for the algorithmic analysis, fabrication, and adhesive assembly methods that promise to reduce production time and aid in the scalability of the system.
Date
May 2018 – August 2019
Project Type
Academic Research & Pavilion
Institution
HiLo Lab – University of British Columbia School of Architecture and Landscape Architecture
Team
Blair Satterfield (Director)
Alex Preiss (Research Assistant)
Derek Mavis (Research Assistant)
Graham Entwistle (Digifab Assistant)
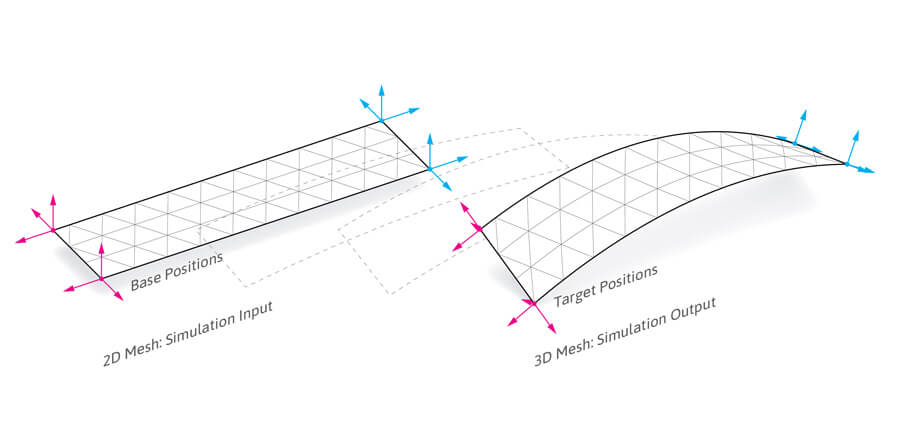
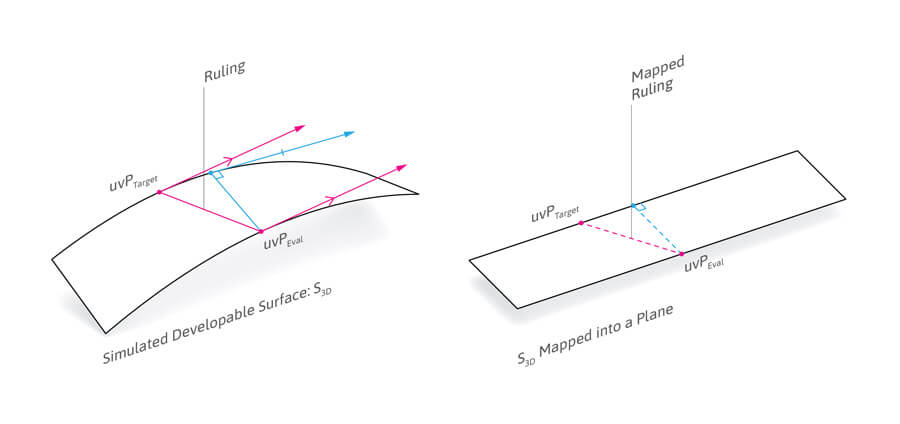
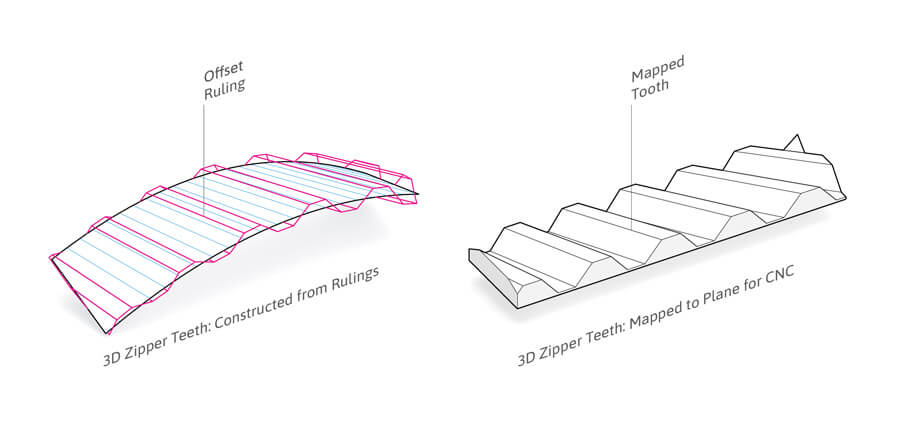
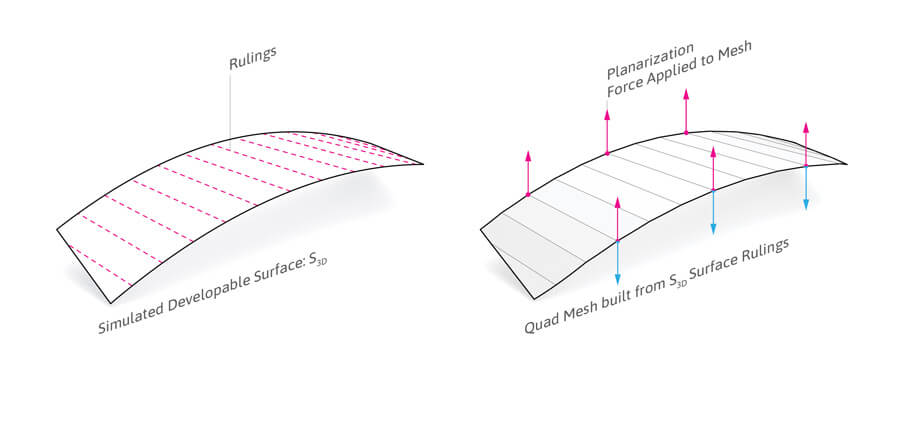

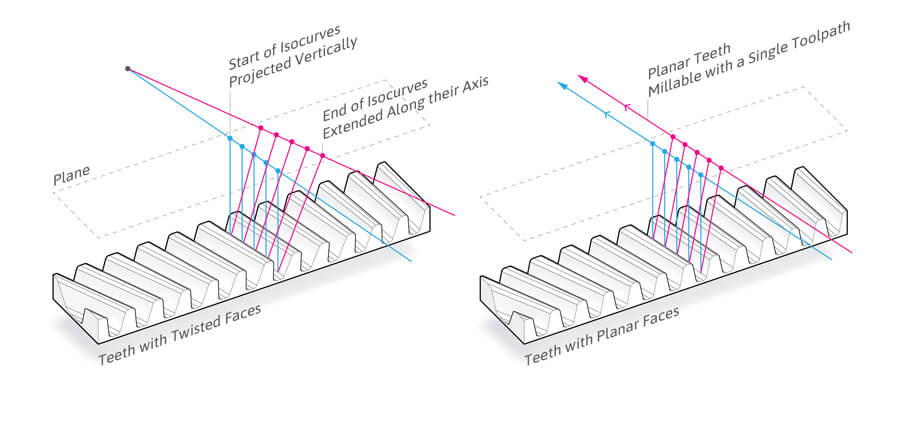